Show:
Future-Proofing Manufacturing: Tech And Strategy Integration
The manufacturing sector is evolving rapidly with technological advances. To stay ahead, businesses must engage in future-proofing practices by integrating cutting-edge technology with strategic foresight.
In this article, you can explore the critical components of a future-proof manufacturing strategy and how technology intertwines with this vision, ensuring a sustainable and robust industrial future.
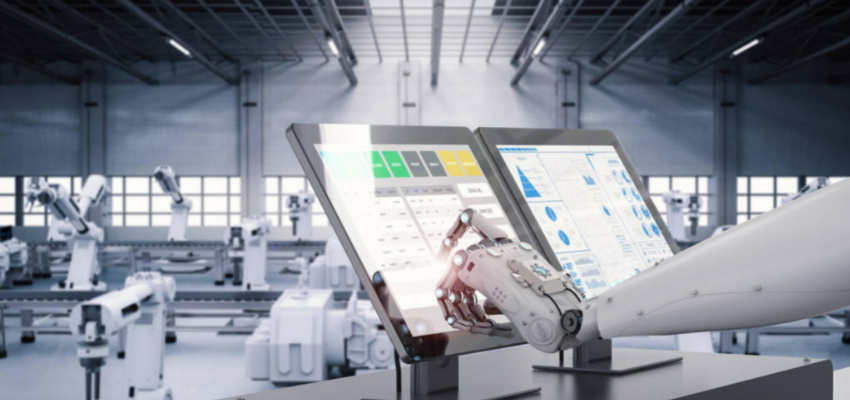
Understanding Future-Proofing In Manufacturing
Future-proofing is about preparing for the unknown. For manufacturing, this means employing technologies and strategies that prime production and business models for future challenges. The aim is to cultivate a resilient ecosystem, ready to adapt and thrive in the face of change.
Consider cloud manufacturing ERP systems. These are not merely digital tools; they embody a strategic shift toward agility and insight. A cloud-based ERP is more than an operational choice—it’s a commitment to continuous adaptation, scaling with ease, and safeguarding data.
The Role Of Technology In Fortifying Manufacturing
Technology is the backbone of modern manufacturing’s resilience. Below, we explore how various technologies contribute to this goal:
- Digital Twins And Simulation: These virtual models empower manufacturers to experiment and fine-tune without physical risk. They are crucial for predictive maintenance, efficiency, and rapid innovation.
Take, for instance, a boutique bicycle manufacturer that uses digital twins to optimize the design of a new lightweight frame. By simulating stress tests and airflow, they achieve perfection in design without expending resources on multiple prototypes.
- Internet Of Things (IoT): IoT’s real-time monitoring capabilities revolutionize maintenance and production quality.
Picture a tooling company using IoT sensors to track wear on machinery, forecasting the need for parts replacement. This foresight is invaluable in minimizing downtime and maintaining production integrity.
- Artificial Intelligence (AI) And Machine Learning (ML): These are the silent powerhouses of data analysis, providing insights that drive real-time decision-making, predictive maintenance, and even fully autonomous operations.
A retail distributor could leverage AI to fine-tune inventory levels, reducing waste and ensuring product availability aligns with demand patterns.
- Advanced Robotics And Automation: Beyond repetitive tasks, modern robots can learn and adapt, enhancing production lines with their flexibility.
An automotive parts manufacturer could deploy such robots to seamlessly transition between product types, dramatically reducing the changeover time typically lost to retooling. These automated tools are capable of all sorts of tasks, and there are manufacturers of polishing robots as well as those focusing on hardware intended for welding, painting, packaging and much more besides.
- Additive Manufacturing (3D Printing): This technology expands the creative horizons of prototyping and production, facilitating the manufacture of designs once deemed too complex or costly.
A jewelry maker could utilize 3D printing to materialize intricate designs directly from the drawing board, offering unprecedented customization.
Integrating these innovations with a cloud manufacturing ERP system enables businesses to operate with improved efficiency and agility, positioning them well for future advancements.

Collaborative Ecosystems In Smart Manufacturing
The digitization of manufacturing opens up new avenues for collaboration across the entire value chain. By leveraging interconnected platforms, manufacturers can forge closer relationships with suppliers, partners, and customers, creating a more responsive and innovative production ecosystem.
- Integrated Supply Chains: Smart manufacturing dissolves the barriers between different stages of production. By sharing data and insights across the supply chain, companies can anticipate demand shifts and respond swiftly.
- Co-Innovation Hubs: Spaces where manufacturers, technology experts, and creative minds converge to push the boundaries of what’s possible. These hubs serve as catalysts for shared innovation, driving the industry forward.
- Customer-Centric Production Networks: Utilizing direct customer feedback and data analysis, manufacturers can customize their offerings more precisely, enhancing customer satisfaction and loyalty.
- Digital Marketplaces And On-Demand Manufacturing: The rise of online platforms that connect manufacturers directly with end users and fabricators has transformed traditional production models. On-demand manufacturing supports a more sustainable approach by reducing excess production and enabling smaller businesses to compete on a larger scale. This access to digital marketplaces also facilitates rapid prototyping, and small-batch production runs crucial for niche markets and bespoke product creation.
Adopting a collaborative approach is essential for enduring success in manufacturing. Engaging in these interconnected networks positions businesses as drivers of industry evolution, not merely bystanders to change.
Strategic Integration: The Path Forward
The successful integration of technology into manufacturing strategies requires a holistic approach:
- Invest in Training And Skills Development: Equip your workforce with the skills to manage and interact with new technologies. Continuous learning and upskilling are vital for the adaptability of your team.
- Embrace Data-Driven Decision Making: Utilize the data to make informed strategic decisions. Cultivate a culture that values evidence-based approaches over intuition alone.
- Innovate With The Customer In Mind: Keep the end-user in mind when innovating. Develop products and solutions that meet evolving customer needs and create value.
- Practice Sustainability: Future-proofing also means being environmentally responsible. Implement sustainable practices that minimize your carbon footprint and comply with regulations, ensuring longevity.
- Take Cybersecurity Measures: As manufacturing grows more connected, the risk of cyber threats increases. Robust cybersecurity protocols are essential to protect sensitive data and intellectual property.
- Leverage Cross-Functional Collaboration: Foster an environment where different departments work together to implement new technologies. This cross-functional collaboration ensures all aspects of the business are aligned and moving forward together.
Challenges And Considerations
While the benefits are clear, future-proofing has its challenges. It requires significant investment, a willingness to change, and a strategic approach to implementation. Additionally, manufacturers must consider:
- Tech Growth: Tech must be able to grow with the business. It’s vital to choose systems that can scale up as needed.
- System Compatibility: New tech has to work well with what’s already there. Seamless integration is key.
- Financial Considerations: Beyond the initial investment, the financial model must account for the total cost of ownership of new technologies, including unexpected costs that may arise from integration issues or rapid technological changes.
- Supply Chain Dynamics: In a connected manufacturing environment, it’s crucial to evaluate and secure the entire supply chain. Disruptions in one part can cascade, so resilience and responsiveness are key.
- Quality Control: New technologies should enhance, not compromise, the quality of the products. Continuous monitoring and control mechanisms must be implemented to maintain product standards.
- Regulatory Compliance: Keep abreast of and comply with the latest industry regulations that pertain to new technologies. This ensures that as the business advances technologically, it does not fall foul of legislative changes and maintains its market standing.
By acknowledging and preparing for these challenges, manufacturers can pave a more reliable path toward a technologically advanced and strategically secure future.
Final Thoughts
For manufacturers to thrive, integrating advanced technologies with strategic planning is non-negotiable. Reflect on how your business will navigate the evolving landscape of manufacturing.